Endurance Calculations for Bearings
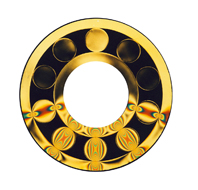
By Daniel R. Snyder, SKF USA, USA .
{access view=!registered}Only logged in users can view the full text of the article.{/access}{access view=registered}
The industry turns to standardised life calculations for good reason: it is realistically impractical from a time and cost perspective to test the number of bearings for a specific application and its operating conditions for required acceptable confidence.A growing list of factors relevant for bearing life calculations have been integrated over the years in keeping with an increasing understanding about operating conditions and the related ‘system’ influences of solid contamination, lubrication, operation regimes, internal stresses from mounting, residual stresses from hardening and other manufacturing processes, the material cleanness, matrix and fatigue stress limit, and others.
The evolution of standards has been to refine the life calculation methods to predict more accurately the actual life in a specific application, given certain operating parameters: in other words, a closer match of the calculated life with the experienced service life. Recent scientific advances in bearing manufacturing, tribology, materials, end-user condition monitoring and computation abilities have led to more sophisticated and accurate bearing life calculation possibilities.
In 2007, ISO (the International Organization for Standardization) published a revised ISO 281 standard further advancing the capabilities for life calculations by including a bearing material’s fatigue stress limit and a factor for the effect of solid contamination for different lubrication systems (such as grease, circulating oil, oil bath and others) on bearing life.
In defining the term ‘life’, several types often will be referenced.
A bearing’s basic life or its L10 (as defined in ISO and ABMA standards) is based on the life that 90% of a sufficiently large group of apparently identical bearings can be expected to attain or exceed. The median or average life (sometimes called MTBF, or Mean Time Between Failure) is approximately five times the calculated basic rating life. Service life represents the actual life of a bearing in real operating conditions before it fails or is deemed necessary to be replaced for whatever reason. The specification life is generally a requisite L10 basic rating life and is grounded in a manufacturer’s experience with similar applications.
Getting Started
Bearing selection is usually based on bearing life and rolling contact fatigue models to predict the life. Therefore, selection of initial bearing size for an application normally starts by comparing its load ratings to the applied loads that generate fatigue, causing stresses with regard to the requirements for service life and reliability. Both dynamic and static bearing load conditions must be independently verified.
The basic dynamic load rating will be used for life calculations involving dynamically stressed bearings, such as those bearings that will rotate under load. This rating defined in ISO 281 expresses the bearing load that will provide a basic rating life (L10) of 1 million revolutions. Dynamic loads should be checked using a representative duty cycle or spectrum of load conditions on the bearing, including any peak (heavy) loads that may possibly occur.
The basic static load rating applies to calculations when the bearings will rotate at speeds less than 10rpm, become subjected to very slow oscillating movements, or will remain stationary under load during certain periods. Static loads are not only those applied with the bearing at rest or at very low rotational speeds, but should factor in the static safety of heavy shock loads (very short duration loads). Excessive static loads can compromise the integrity of a bearing by causing plastic deformations on the contact surfaces.
The loads acting on a bearing can be calculated according to classical mechanics if the external forces are known or can be calculated. As examples, these external forces may include resultant forces from power transmission, shaft or housing supports, or inertia effects.
When calculating the load components for a single bearing, the shaft is assumed to be a beam resting on rigid, moment-free supports. In basic catalogue or simplified calculations, elastic deformations in the bearing, the housing, or the machine frame usually are not considered, nor are the moments produced in the bearing as a result of shaft deflection. Historically, standardised methods for calculating basic load ratings and equivalent bearing loads are grounded in similar assumptions for the sake of simplification.
If the calculated bearing load fulfils the requirements for the basic dynamic load rating (meaning the load is constant in magnitude and direction and acts radially on a radial bearing or axially and centrically on a thrust bearing), then the load may be inserted directly into the life equations.
In all other cases, an equivalent dynamic bearing load should be ascertained. This is defined as the hypothetical load (constant in magnitude and direction and acting radially on radial bearings or axially on thrust bearings), which, if applied, would exert the same influence on bearing life as the actual loads to which the bearing is subjected.
Radial bearings often are subjected to simultaneously acting radial and axial loads. If the resulting load is constant both in magnitude and direction, the equivalent dynamic bearing load can be obtained from the equation:
P = XFr + YFa
where
P = equivalent dynamic bearing load
Fr = actual radial bearing load
Fa = actual axial bearing load
X = radial load factor for the bearing
Y = axial load factor for the bearing
An additional axial load only influences the equivalent dynamic load P for a single row radial bearing if the ratio Fa/Fr exceeds a certain limiting value. With double row radial bearings even light axial loads are significant.
The same general equation is also applied for spherical thrust bearings and other thrust types that can take both axial and radial loads. For thrust ball bearings and other types that can carry only purely axial loads, the equation can be simplified (P = Fa), provided the load acts centrically. For thrust bearings that support both axial and radial loads, designs vary such that manufacturers’ catalogues need to be consulted.
Basic Rating Life Equation
The calculation of bearing life has its roots back almost 60 years ago, when Gustaf Lundberg from Chalmers Institute of Technology and Arvid Palmgren from bearing company AB SKF applied the Weibull probability theory of fatigue to the calculation of rolling bearing life. Their fundamental assumptions and derivations in 1947 and 1952 regarding internal load distribution, equivalent loads and Weibull statistical distribution of bearing life form the basis for ANSI/ABMA and ISO life rating standards and most bearing manufacturers’ catalogues.
First adopted by ISO in 1962, the simplest method for bearing life calculation is represented by the ISO 281 or ABMA Standards 9 and 11 equation for basic non-adjusted rating life:
L10 = (C/P)p or C/P = L10 1/p
where
L10 = basic rating life, millions of revolutions
C = basic dynamic load rating
P = equivalent dynamic bearing load
p = exponent of the life equation
(p = 3 for ball bearings and p = 10/3 for roller bearings)
For bearings operating at constant speed it may be more convenient to deal with a basic rating life expressed in operating hours using the equation:
L10h = 1,000,000/60 n (C/P)p
or
L10h = 1,000,000/60 n L10
where
L10h = basic rating, operating hours
n = rotational speed (rpm)
As an application example, a deep groove ball bearing operating in an electric motor at 3,600rpm is subjected to a radial load of 100lbs (45.36kg). To calculate the L10h:
n = 3,600rpm
P = 100 lbs
C = 3,330lbs (from manufacturer’s catalogues or other supplied information)
p = 3 (for ball bearing)
Using these values and the ‘operating hours’ equation, the basic life expressed in hours for the bearing in this case would be 166,375 hours.
Since individual bearing life can only be predicted statistically, it is especially important to consider that life calculations refer only to a bearing population and a given degree of reliability. The basic rating life L10 is associated with 90% reliability using bearings made from high-quality material, exhibiting good manufacturing quality, and performing in conventional operating conditions.
In practice, of course, the basic rating life may deviate significantly from the actual service life in a given application. As an example, published results have shown that actual tested life can deviate from the basic rating life by a factor of nearly five times. ‘Service life’, then, represents the actual life of a bearing in real operating conditions before it fails.
‘Service life’ further underscores that field failures can result from ‘root causes’ instead of bearing fatigue. While the bearing is the victim and has failed, most times today it is the abnormal stresses in the bearing as a result of poor operating environments leading to the failure. Examples of root causes include contamination, wear, misalignment, corrosion, mounting damage, lubrication or sealing systems.
Over the years science and bearing technology advances have resulted in improved designs and manufacturing processes to extend bearing life and reduce their sensitivity to severe operating conditions. Calculation methods have followed suit to predict service life more accurately. The ISO bearing rating and life calculation standard (ISO 281) has developed along with these advances as bearing manufacturers and users universally accepted and used newer technologies.
Examples of related progress are inclusion of a reliability factor to adjust life for those applications requiring higher reliability; a factor on life considering the effects of lubricant and lubrication operating conditions; increased load ratings accounting for better material properties and manufacturing processes; and, in 2000, recognition of a fatigue stress limit for bearing steels and the effects of solid contamination on bearing life.
The new revision to the ISO rating and life standard (ISO 281) offers a modified life equation along with agreed-upon calculation methods for high-quality bearings to supplement the basic rating life. This will account for the lubrication and contamination condition of the bearing and the fatigue limit of the material.
While the individual bearing manufacturer should be consulted on the applicable specifics, the following new equation expresses modified life in operating hours (when speed is constant):
Lnm = a1aISOL10
where
Lnm = manufacturer’s rating life (at n% reliability), millions of revolutions (C/P)p
Lnmh = manufacturer’s rating life (at n% reliability) operating hours
L10 = basic rating life (at 90% reliability), millions of revolutions
a1 = life adjustment factor for reliability (1.0 for 90% reliability)
aISO = manufacturer’s life modification factor according to ISO 281
The determination of aISO involves the use of a contamination factor based on the lubrication system and cleanliness class of the lubricant system as defined in ISO 4406. Graphs for different cleanliness classes considering bearing size and lubrication operating conditions are provided. This contamination factor is then used along with the ratio of the bearing fatigue load limit to the bearing equivalent load limit and the lubrication condition to determine a life adjustment factor, aISO.
Generally, the better the lubrication condition and lower the equivalent load, the less sensitive a bearing will be to contamination levels. Conversely, the higher the load and the poorer the lubrication condition, the more sensitive bearing life is to contamination cleanliness level.
Advantages and Caution
The bearing life calculated according to the new methods (whether the new ISO 281 or similar methodology offered by individual bearing manufacturers) today greatly enhances a user’s ability to predict and ascertain the actual service life with known operating conditions to a much greater extent.
This leads to a variety of advantages:
- The possibility to downsize a bearing under good operating conditions to reduce friction, energy and weight.
- Select lubrication and filtration to maximise bearing and system life.
- Extended warranties or service intervals under controlled operating conditions.
- Ability to better evaluate the influence of operating parameters on specific bearing types and designs.
- The calculations are sensitive to operating conditions of load, temperature, lubrication condition and contamination. If improper operating conditions are used in conjunction with bearing selection it could lead to premature bearing problems.
- The methodology and calculations assume bearings are made according to modern designs, manufacturing processes and bearing material specifications.
- The bearings are installed and maintained correctly.