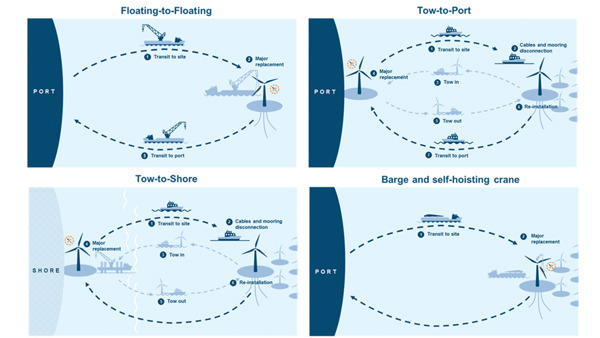
This article details the current state of O&M in floating wind with a particular focus on major component replacement strategies. It summarises year-long discussions held by the expert members of the World Forum Offshore Wind.
By Ilmas Bayati, Peak Wind, Denmark
Like all renewable energy projects, floating offshore wind (FOW) requires O&M strategies tailored towards the specific technology’s characteristics. Floating wind farms will be located further away from the shore, so logistics and workability aspects will bring about extensive maintenance challenges.
Furthermore, dimensions of wind turbines are growing, which means that major components are going to be heavier and positioned at greater heights.
Currently, bottom-fixed turbines are installed by wind farm installation vessels based on jack-up technologies. Because floating wind farms are located in deeper waters, it will often not be possible to use the jack-up principle for floating turbine installations.
There are a few possible solutions to consider for major component replacement (MCR) depending on where it takes place, i.e. on- or off-site (see Figure 1).
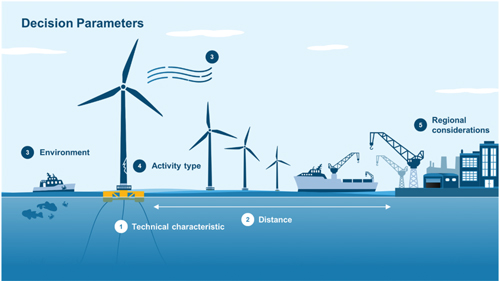
Off-site repair means disconnecting the floating offshore wind turbine (FOWT) system from the project site and towing it to a secondary area (a port or an area close to shore) for the major repair. The two off-site repair options are tow-to-port and tow-to-shore.
Tow-to-Port
This strategy relates to an onshore (dry-dock or inshore) overhaul. This means that the replacement would be executed onshore, thus off-site; however, the replacement can only happen after a reversed-installation process has been carried out, which includes towing the unit to the harbour. The FOWT is towed by readily available and relatively inexpensive vessels and then repaired with cranage in the typically less harsh onshore weather.
This strategy relates to an onshore (dry-dock or inshore) overhaul. This means that the replacement would be executed onshore, thus off-site; however, the replacement can only happen after a reversed-installation process has been carried out, which includes towing the unit to the harbour. The FOWT is towed by readily available and relatively inexpensive vessels and then repaired with cranage in the typically less harsh onshore weather.
This procedure can be complex, lengthy, and costly, both in terms of operations and downtime. It also requires MCR capabilities at the O&M sites (which are not always available). Currently, this is the main option considered in the floating wind business cases, primarily due to the lack of infrastructure for the on-site scenarios listed later.
Tow-to-Shore
Tow-to-shore is a hybrid solution combining the reverse-installation procedure of the tow-to-port strategy; however, in this case, the unit is towed closer to shore, where a fixed jack-up vessel is installed. This strategy can be considered when there are suitable project conditions and/or synergies with other bottom-fixed assets. This is because it has geographic and floater-specific applications.
Tow-to-shore is a hybrid solution combining the reverse-installation procedure of the tow-to-port strategy; however, in this case, the unit is towed closer to shore, where a fixed jack-up vessel is installed. This strategy can be considered when there are suitable project conditions and/or synergies with other bottom-fixed assets. This is because it has geographic and floater-specific applications.
This strategy may be more costly in comparison with an onshore crane due to the rental of the jack-up vessel. It may also be challenging from a consenting point of view, as the project would have to obtain authorisation to work outside the designated project area and potentially coordinate with different marine space users.
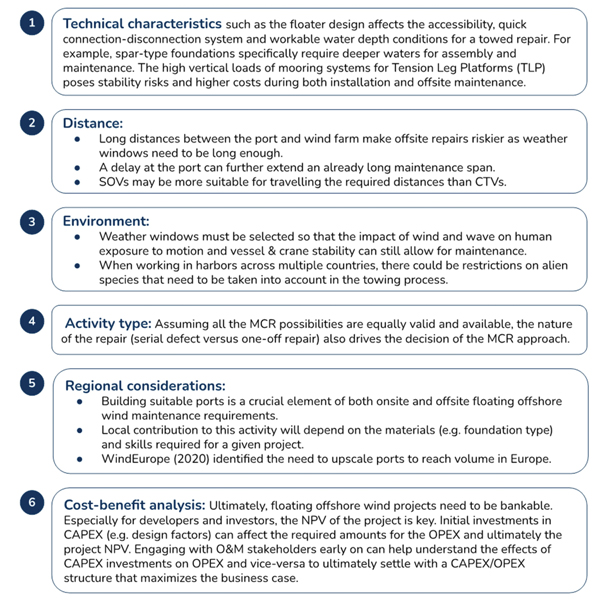
On-site Strategies
Alternatively, MCR can be performed on-site. This would mean performing the MCR at the project site with the help of specialised vessels and cranage. Two possible strategies for on-site MCR are floating-to-floating and self-hoisting equipment.
Alternatively, MCR can be performed on-site. This would mean performing the MCR at the project site with the help of specialised vessels and cranage. Two possible strategies for on-site MCR are floating-to-floating and self-hoisting equipment.
Floating-to-Floating
The floating-to-floating scenario relates to offshore overhaul, meaning that the replacement will be solely carried out on-site. A heavy lift vessel located at the wind farm site is equipped with cranage that can transfer components to and from the FOWT directly.
The floating-to-floating scenario relates to offshore overhaul, meaning that the replacement will be solely carried out on-site. A heavy lift vessel located at the wind farm site is equipped with cranage that can transfer components to and from the FOWT directly.
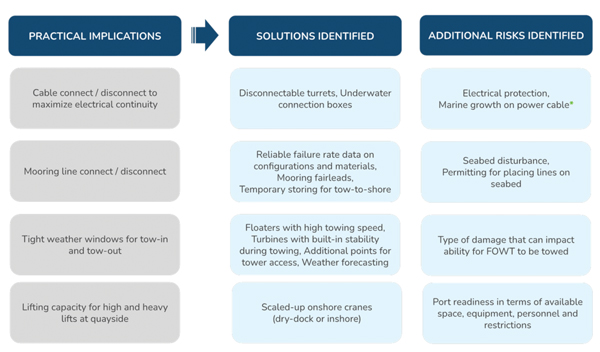
An important and prompt evolution of the maritime industry is required to make this scenario a reality. There is a clear need for acceleration with new designs in order to provide vessels and solutions capable of carrying out the replacement operations in a floating-to-floating set-up. These need to be efficient, quick and operated directly by the floating wind unit. Until the floating-to-floating solution can confidently rely on a newly developed maritime/vessel industry, the tow-to-port option remains most considered in floating wind business cases.
Self-Hoisting Equipment
This solution aims to utilise new self-hoisting or climbing cranes for the replacement of major components without requiring vessels other than a support barge (or similar) at the site or involving expensive tow-to-port operations. The adoption of different types of crane technology / vessel combinations is now being discussed as the technological development progresses and new companies approach the market.
This solution aims to utilise new self-hoisting or climbing cranes for the replacement of major components without requiring vessels other than a support barge (or similar) at the site or involving expensive tow-to-port operations. The adoption of different types of crane technology / vessel combinations is now being discussed as the technological development progresses and new companies approach the market.
This opens up discussion around lifting capacity, operations time at sea, responsibilities of original equipment manufacturers (OEMs), etc. Improvements to worker environments are also required, especially regarding access to tower, weather windows and the weight of equipment.
Decision Parameters
From a technical standpoint, risks and their associated mitigation plans must be considered. From an economic standpoint, the cost of operation as well as the cost of lost revenue (from time without electricity generation of the floating system(s)) will influence the chosen maintenance strategy. The World Forum Offshore Wind (WFO) Subcommittee has provided a decision framework of parameters for project-specific evaluation and analysis (see Figures 2a and 2b).
From a technical standpoint, risks and their associated mitigation plans must be considered. From an economic standpoint, the cost of operation as well as the cost of lost revenue (from time without electricity generation of the floating system(s)) will influence the chosen maintenance strategy. The World Forum Offshore Wind (WFO) Subcommittee has provided a decision framework of parameters for project-specific evaluation and analysis (see Figures 2a and 2b).
Off-site Maintenance Analysis
Off-site maintenance is an opportunity to perform work in a controlled area and to work with more readily available equipment than with floating-to-floating vessels and cranes working in dynamic conditions. Figure 3 summarises some key considerations for procedures in an off-site operation.
Off-site maintenance is an opportunity to perform work in a controlled area and to work with more readily available equipment than with floating-to-floating vessels and cranes working in dynamic conditions. Figure 3 summarises some key considerations for procedures in an off-site operation.
The suitability of off-site maintenance varies depending upon the floater system and corresponding mooring configuration. Studies have identified semi-submersibles as benefiting most from tow-to-port technologies.
It is important to stress that the port requirements such as size/depth, bearing capacity, cranage, and spare part availability are crucial to an off-site strategy. In particular, the Carbon Trust has identified ‘quay load-bearing capacity’ as one of the most important port requirements. Integrating installation and O&M considerations at the early stages of a project involves port stakeholders who need to know how to adapt their landscape to fabricate, assemble, install and maintain – and ultimately support the industry of – floating wind turbines.
O&M over the Project Lifetime
The promotion of new technologies is key to realising the O&M needs of future floating wind projects. In addition, early engagement of O&M players in a FOW project can improve alignment across all project stakeholders and secure an optimal set-up for the entire duration of the project.
The promotion of new technologies is key to realising the O&M needs of future floating wind projects. In addition, early engagement of O&M players in a FOW project can improve alignment across all project stakeholders and secure an optimal set-up for the entire duration of the project.
The following are three important considerations that project leaders and stakeholders need to have in mind for future projects:
Industry leaders need to push for the new technologies required for commercial floating wind.
Major developers and floating platform technology providers have the capacity to push for innovations such as digital twinning solutions, quick connection–disconnection technology and, to an extent, floating-to-floating vessels, at the required scale. Applying new technologies as early as possible (e.g. on demonstration projects) can initiate a track record and benefit commercial projects sooner. Promoting research and development in vessel technology, such as floating cranes and opened-up control strategies, is crucial to make on-site maintenance a feasible option in the future.
Major developers and floating platform technology providers have the capacity to push for innovations such as digital twinning solutions, quick connection–disconnection technology and, to an extent, floating-to-floating vessels, at the required scale. Applying new technologies as early as possible (e.g. on demonstration projects) can initiate a track record and benefit commercial projects sooner. Promoting research and development in vessel technology, such as floating cranes and opened-up control strategies, is crucial to make on-site maintenance a feasible option in the future.
A more integrated design process is required to optimise systems and improve real-time monitoring operations
From an O&M and logistics concept perspective, settling O&M aspects at the design stage of a project could be achieved with early communication and coordination. The earlier the O&M perspective can be integrated into the EPCI contract, the better influence it can have on the chosen O&M strategy.
From an O&M and logistics concept perspective, settling O&M aspects at the design stage of a project could be achieved with early communication and coordination. The earlier the O&M perspective can be integrated into the EPCI contract, the better influence it can have on the chosen O&M strategy.
From a design perspective, the integration of turbines and floaters as well as vessels and their control systems can help make systems more lightweight, reduce safety factors, and accommodate holistic monitoring operations. As these affect O&M practices in the project’s lifetime, they should be integrated at the design stage. Data confidentiality of the behaviour of components is viewed as a bottleneck for deploying advanced monitoring technology for preventive maintenance. Collaboration between stakeholders will be necessary to make real-time monitoring operations possible, all within a framework of respecting intellectual property rights and preserving competition.
Projects must approach new technologies without affecting the safety factor for insurability
From an insurance perspective, there is a risk in insuring projects where the applied O&M strategy includes new technologies and methodologies and is new to the contractor. This will likely make insurance companies reluctant to insure, especially since they would rather see a track record in the tools and methods applied.
From an insurance perspective, there is a risk in insuring projects where the applied O&M strategy includes new technologies and methodologies and is new to the contractor. This will likely make insurance companies reluctant to insure, especially since they would rather see a track record in the tools and methods applied.
To reconcile the advantages of using existing experience with the need to work with new technology, a project manager can consider:
- Experience from bottom-fixed or oil and gas that should be used to the fullest to facilitate the underwriting of a project
- Transparency on the developer’s side – important for insurers to properly evaluate project risks and mitigation strategies involving newer technology and/or materials
- Risk sharing as a way to spread costs and risks of new maintenance approaches
- Incorporating new technologies early on but in a way that increases the factor of safety (or ensures some redundancy) to promote the spread of risk responsibility and improve the availability guarantee in a project contract
- A spare parts concept that secures prompt replacement of the damaged or lost items, thus reducing the loss of energy production.
Preliminary Conclusions
The outcomes of the discussions in the WFO Floating Offshore Wind O&M Subcommittee showed pertinent interest in on-site repair strategies. These on-site approaches, namely floating-to-floating and self-hoisting equipment, are expected to perform major component exchanges in the longer term but require serious evolution in the vessel and cranage industries.
The outcomes of the discussions in the WFO Floating Offshore Wind O&M Subcommittee showed pertinent interest in on-site repair strategies. These on-site approaches, namely floating-to-floating and self-hoisting equipment, are expected to perform major component exchanges in the longer term but require serious evolution in the vessel and cranage industries.
The mobilisation of resources and investments to develop FOW O&M solutions requires capable actors to take the lead. Notably, OEMs, floating platform technology providers, and developers were identified as the players that can (and should) spearhead the development of new floating wind O&M tools and solutions.
Commercial-scale floating wind projects will ask for a reorganisation of the ways project sub-packages communicate with each other and share information. The O&M phase is a ‘gluing’ factor for all the different efforts involved in designing, building, insuring and commissioning a FOW project, and so studying its aspects at the pre-commercial stage of the industry we are in now will help achieve a sustainable large scale.
Further Reading
https://wfo-global.org/wp-content/uploads/2021/12/WFO_OM-WhitePaper-December2021-FINAL.pdf
https://wfo-global.org/wp-content/uploads/2021/12/WFO_OM-WhitePaper-December2021-FINAL.pdf
Biography of the Author
Ilmas Bayati is a professional with 10+ years of experience in renewable energy systems, oil and gas, and infrastructures, with a technical background in floating/offshore wind. He is Head of Floating Wind Excellence at Peak Wind and is also Chairman of the Operations and Maintenance Committee at the World Forum Offshore Wind. He obtained a PhD in the dynamics of mechanical systems from Politecnico di Milano, Italy, focusing on the aero-hydrodynamics of floating offshore structures and has a master in business administration (MBA) from Rotterdam School of Management, the Netherlands.
Ilmas Bayati is a professional with 10+ years of experience in renewable energy systems, oil and gas, and infrastructures, with a technical background in floating/offshore wind. He is Head of Floating Wind Excellence at Peak Wind and is also Chairman of the Operations and Maintenance Committee at the World Forum Offshore Wind. He obtained a PhD in the dynamics of mechanical systems from Politecnico di Milano, Italy, focusing on the aero-hydrodynamics of floating offshore structures and has a master in business administration (MBA) from Rotterdam School of Management, the Netherlands.
Contact
https://peak-wind.com/